… is the mathematical “taking apart” of a real system to examine its defined individual mathematical elements. Then, synthesis is utilized to collect the calculated answers into an understandable report that suggests a rational organized path forward to solve an observed problem. Along the solution’s progress, the four step Galambosian Scientific method is used:
- Observation
- Hypothesis Formulation
- Extend the Hypothesis
- Observe Again
For example, many planned and installed system designs do not consider enough temperature/pressure differentials, especially during non-equilibrium conditions such as start-up, shut-down, rapid restart, loss of plant power, or other normal or upset conditions. In situations like these, system elements such as lubrication systems, gas flows, and vessel nozzles, foundations, piping flanges, spring supports, rigid supports and other system elements can be overloaded above the levels originally anticipated by the designer. PAI ENGINEERING has years of experience in adapting original designs to withstand non-equilibrium operating conditions. For more information, please call +1 (225) 292 9709.
Stress/Flexibility Analysis
The analysis of piping stress and flexibility lies at the core of our business. We find that unexpected mechanical problems requiring frequent maintenance and/or shut-downs are often caused by an insufficient level of quality in the design of the connected piping system and related structures. Efficiency and therefore profitability suffer, leading ultimately to permanent damage and high costs for repair and maintenance.
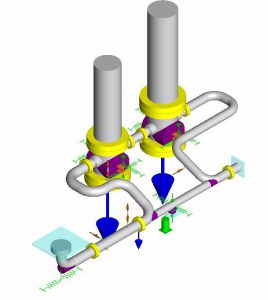
Failure Analysis
A major part of our business activity is reviewing design failures, sometimes after a damage-producing incident. Although many design issues can lead to a piping system failure, the three main causes are:
1. poor original design
2. changed design conditions
3. a need for additional calculations beyond official requirements
Finite Element Analysis (FEA)
For detailed analysis of piping components such as tube sheets, branch connections, nozzle connections, flanges, tees, lifting lugs or another program definable object which may be under undesirably heavy loads and/or stresses, we use discretized finite element techniques and software to examine the numerous elements of the object.
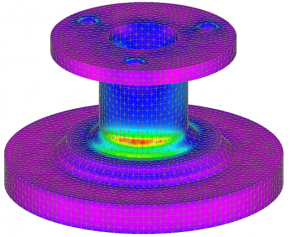
CFD/Fluid Flow Analysis
CFD is a discipline that solves a set of equations governing fluid flow in, over or through any geometrical configuration. CFD is closely linked with other piping stress analysis programs in that they often share use of the finite element method and have similar origins.
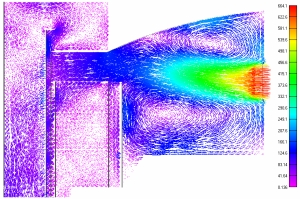
Heat Transfer Analysis
Heat transfer calculations are especially beneficial in determining temperature gradients through pressure containing boundaries when unexplained cracks and/or leaks appear. Heat transfer calculations are also beneficial in determining temperature differentials which occur in piping and/or equipment during non-equilibrium conditions. Such differentials produce distortion stresses and strains that can become very important for proper operations.
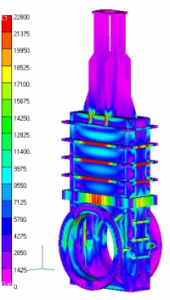
Vibration Analysis
Vibrations are undesirable in most systems and are often the cause of cumulative fatigue damage. Vibrations can become an insidious problem because, depending on their amplitude and frequency, these time-dependent effects can cause rapid open failures such as cracks. Some vibrations may never lead to an open failure, but can wreak havoc on rotating equipment such as pumps, turbines and compressors.